What is servo Drive & How to Works it? what is servo motor
What is servo How to Works it? A servo is a compact and cost-effective actuator or motor that is commonly utilized in small-scale robotics projects and radio control systems. These devices are mass-produced for widespread use in various applications. Most servos are rotary actuators, although linear actuators are sometimes used as well. Some specialized servos can rotate continuously, originally designed as sail winches for model yachts. A typical servo consists of a small electric motor connected to a train of reduction gears. A potentiometer is attached to the output shaft, which provides feedback on the position of the servo. Some simple electronics create a closed-loop servomechanism. However for details click here What is servo Drive & How to Works it? see the details
The servo’s position, as indicated by the potentiometer, is consistently checked against the desired position set by the control system (e.g. a radio controller). Any difference between the actual and commanded position generates an error signal that drives the motor forwards or backwards to move the output shaft to the desired position. Once the servo reaches the commanded position, the error signal goes to zero and the motor stops. Most modern servos are proportional servos, where the commanded position can be anywhere within the full range of motion. Older servos and an earlier device known as an escapement were only able to move to a fixed set of predetermined positions.
What do servos do? What is servo How to Works it?
Basically, What is servo How to Works it? the Servo systems in industrial motion control are essential. Because servos play an important role in improving transient response times, decreasing steady-state errors, and reducing sensitivity to load variations. To enhance transient response time, the systems of servos typically boost the system bandwidth. They employ feedback mechanisms to track the servo’s position during movement, enabling precise positioning based on control signals. In industrial settings, robotic vehicles utilize servo motors to govern their wheels, ensuring the necessary torque for movement, starting, stopping, and speed control. Moreover, in CNC machining, servos or servo motors are pivotal for precisely controlling the speed and position of cutting tools in CNC machines, thereby enhancing accuracy and efficiency in machining operations.
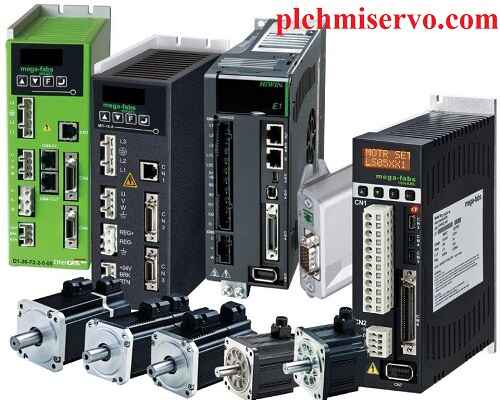
What is a servo motor used for?
A Servo Motor is used for the following key applications:
+Robotics: Servo motors are used in robotics to activate movements, giving the arm its precise angle.
+Conveyor Belts: Servo motors are used to start, move, and stop conveyor belts carrying products along various stages, such as product labeling, bottling, and packaging.
+Camera Lens Correction: Servo motors are built into cameras to correct the lens and improve out-of-focus images.
+Robotic Vehicles: Servo motors are used in robotic vehicles to control the wheels, providing the torque needed to move, start, stop, and control the speed of the vehicle.
+Solar Tracking Systems: Servo motors are used in solar tracking systems to correct the angle of the solar panels so that they stay facing the sun.
+Metal Forming and Cutting Machines: Servo motors are used in metal forming and cutting machines to provide specific motion control for milling machines.
+Textiles: Servo motors are used in textiles to control spinning and weaving machines, knitting machines, and looms.
+Automatic Door Openers: Servo motors are used in automatic door openers to control the doors in public places like supermarkets, hospitals, and theaters.
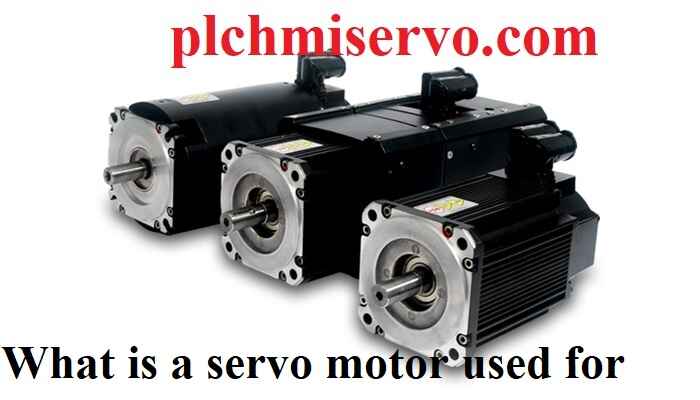
What are servo motor and stepper motor?
A servo motor is a precision instrument in the world of motors. Servo motors are similar to regular continuous motion motors, with both AC and DC versions, as well as brushed and brushless, and synchronous or asynchronous designs. What sets servo motors apart is their feedback loop and drive system. Every servo motor has an encoder and drive controller, where the encoder reports the motor shaft’s position back to the drive controller, creating a closed-loop system. The PLC tells the drive system the desired position and velocity, and the motor’s speed is controlled using typical PWM and sine-wave signals. Adjusting the frequency changes the speed, similar to a typical AC motor, while varying the voltage changes the speed, similar to a DC motor. With an AC servo motor, the drive accepts a signal from the PLC and outputs current at a specific frequency until the desired shaft position is reached.
In contrast, a stepper motor also uses a rotating magnetic field to convert electrical current into rotational motion, but has a much higher density of magnetic poles. Stepper motors break a full rotation into smaller segments, and when a magnetic pole is powered, the output shaft moves by one ‘step’ or segment. Energizing the poles in sequence at a high frequency creates the appearance of smooth rotation, typically done with special output cards that can handle the high frequency. As the number of segments increases, the accuracy of the output shaft position also increases. Stepper motors do not typically require encoders because the segments are accurately divided, and the motor can be commanded to rotate a specific number of degrees.

What are the types of servo motor?
Generally, there are 5 different types of Servo Motors that are commonly used in various industries. Let’s explore these 5 types in detail:
1. DC Servo Motor
DC servo motors have a separate DC source for the field winding and the armature winding. The control can be achieved by either controlling the armature current or the field current. Field control has certain advantages over armature control, and vice versa. DC servo motors often offer precise and quick response to command signals to start/stop because of their minimal armature inductive reactance. They are used in equipment like computerized numerical control (CNC) machines.
2. AC Servo Motor
AC servo motors are AC motors that include an encoder for closed-loop control and feedback. These motors can be positioned with high accuracy and controlled precisely, as required for certain applications. They often have tighter tolerances, better bearings, and may use higher voltages to achieve greater torque. AC servo motors are mostly applied in automation, CNC machinery, robotics, and other applications demanding a high grade of clarity and versatility.
3. Positional Rotation Servo Motor
These motors are the prevalent variety of servo motor. The output shaft rotates approximately 180 degrees. The gear mechanism is equipped with physical stops that prevent it from rotating beyond certain limits in order to safeguard the rotation sensor. These servos are widely used in radio-controlled vehicles, aircraft, robots, toys, and various other applications.
4. Continuous Rotation Servo Motor
Continuous rotation servo motors are similar to the common positional rotation servo motors, but they can rotate indefinitely in either direction. The control signal is interpreted as the speed and direction of rotation, rather than a static position. This type of motor is used in applications like radar dishes, mobile robots, and other scenarios where continuous rotation is required.
5. Linear Servo Motor
Linear servo motors are also similar to the positional rotation servo motors, but they have an additional set of gears to convert the output from circular to back-and-forth linear motion. These servo motors are not as common as the other types, but they can be found in some hobby stores, where they are used as actuators in high-end model aircraft.
What does a servo motor do? What is servo Drive & How to Works it?
A servo motor has built-in ability to rotate very accurately. The key function that sets it apart is its control circuit, which constantly monitors and adjusts the motor’s position. This feedback allows servo motors to perform incredibly precise movements, making them useful for tasks that require the precise control of an object’s angular or linear position, speed, and acceleration, such as automation in factories and robotics. Servo motors work differently than other motors and have different types and abilities. They are used in closed-loop systems consisting of:
+Motor: The motor can be either a DC or AC motor, depending on the power source and specific application needs.
+Gear System: The gear system serves to reduce motor speed, increase torque, and provide feedback to the position sensor.
+Position Sensor: The position sensor, typically a potentiometer, but could also be an encoder, a resolver, or another position-sensing device, converts the feedback from the gear system into an electrical signal.
+Control Circuit: The control circuit, either an analog or digital circuit, decodes the signal from the position sensor, compares it to the desired position, and then adjusts the motor’s rotation to reach that position.
The motor is linked to a gear system that helps to slow down the motor’s speed, boost its torque, and send feedback to a potentiometer. The potentiometer converts the feedback into an electrical signal, which is then transmitted to the control circuit. The control circuit interprets the signal, compares it to the desired position, and adjusts the motor’s rotation to achieve that position.
References:
https://en.wikipedia.org/wiki/Servo_(radio_control)
https://standardbots.com/blog/servo-motors-what-are-they-used-for#:~:text=Robotic%20vehicles
https://control.com/technical-articles/servo-motor-vs-stepper-motor-understanding-the-differences